Double Mechanical Seal With a Mechanical Drive
The MECO EP Type-3 model is a highly versatile split seal for horizontal dryers and reactors in vacuum service. The EP Type-3 is a double mechanical seal, using a mechanical drive to rotate bearing-grade, synthetic seal faces against fixed, stainless steel seal stationary faces. The EP Type-3 is a full-contact, soft face mechanical shaft seal, custom-designed to fit your machinery with little or no modification.
- Fully split
- High axial shaft mobility
- Self-adjusting
- Air-purged
EP Type-3
Details
Description
The MECO EP Type-3 split seal model is most often used on dryers, sigma mixers, plow blenders, paddle blenders, reactor vessels, extruder-compounders and similar rotating equipment used in the chemical, plastics, metals, pharmaceutical and other process industries. The seal addresses the challenges of higher temperatures, large thermal motion, changing pressures and shaft runout. They are frequently used on agitator shafts in reactors where the process medium goes through several phase changes, containing liquids, vapors and/or solids. They are well-suited for extensive thermal growth or shrinkage of the shaft and/or vessel. They are ideal for vacuum service and moderate pressure applications. They may be used for processes where aggressive solvents, hazardous materials and explosive environments are present. They handle the high shaft speeds and shaft runout associated with large extruder-compounders.
How it works
The MECO EP Type-3 seal model utilizes a precision machined split seal housing similar to a stuffing box and gland follower. The MECO-DR or mechanical drive consists of all the rotating seal components. These rotating parts are fitted around the shaft prior to installing the seal housing.
The MECO-DR is comprised of rotating seal faces, braided packing or “O”-rings, pusher rings, drive pins and a drive collar. The MECO-DR mechanical drive attaches only one component, the drive collar, to the shaft. Pusher rings are permitted to float on either side of the drive collar. Large diameter, fixed length drive pins link the two pusher rings a fixed distance from each other with the drive collar positioned between them. The drive collar is set at a predetermined distance from the pusher rings. On the other side of the pusher rings are two sets of braided packing rings followed by the rotating seal faces (rotors). Together, the pusher ring & rotor contain each set of braided packing, forming a static seal to the shaft. The rotor orients the dynamic sealing surface perpendicular to the shaft, permitting radial shaft runout, as compared to a stuffing box and packing which compress the shaft radially. When dictated by application parameters, the packing rings are replaced by “O”-rings fitted between the rotors and the shaft.
The MECO-DR allows the shaft to move axially, sliding on the packing or “O”-rings, limited only by the length of the drive pin. The drive collar locked to the shaft engages the drive pins, transferring the torque from the shaft to the seal faces and allowing the seal to compensate for thermal growth.
The nose or pilot of the gland follower provides the outboard (secondary) stationary seal face. A plate attached to the bottom of the stuffing box provides the inboard (primary) stationary seal face. These are precision machined stationary seal faces (stators) with lapped and polished seal face surfaces.
Maintenance
The MECO EP Type-3 seal model uses compressed inert gas or air as a barrier fluid and diagnostic tool. The gas acts as a barrier to provide pneumatic seal face loading. A pressure gauge is attached to the seal housing to monitor seal cavity pressure. External springs are attached to the back of the gland follower to hold the outboard seal face in check and provide seal face alignment capabilities.
As the sacrificial rotor seal face material wears, the springs will gradually expand and the seal cavity pressure will gradually decrease. After a significant pressure decrease or when an opportunity presents itself, the springs should be reset. Then the pressure will reset itself.
Construction
The MECO EP Type-3 seal’s rugged components are designed for long life. The standard configuration uses stainless steel stationary seal faces. The standard rotor seal faces are MECO 3000, a high performance, bearing grade, polymer filled PTFE with FDA approval. No abrasive filler material is added to the MECO 3000. The housing is either made of a 300 series stainless steel or aluminum. The static rings sealing on the shaft are a dense, FDA-approved PTFE braided packing or an “O”-ring depending on application requirements. The standard elastomer for the O-ring is FDA Viton®. For large shaft diameters or highly-abrasive process materials, a replaceable stator insert, the polished central ring in the photo, can be offered. MECO seals can be fabricated from a wide variety of suitable materials.
Viton® is a registered trademark of E.I. Dupont de Nemours & Company.
Sizes Available
The MECO EP Type-3 seal model is custom-designed and built to order. Dimensions will vary according to each application, but typical dimensions are shown in the illustration below. Having extra axial space is helpful for the installer and maximizes thermal expansion capabilities. EP Type-3 seals are readily designed to fit most mounting arrangements specified by equipment OEMs and are designer-friendly, to interface with customized, in-house process equipment requirements. Seals can be built either to S.A.E or metric dimensions.
Sizing Chart
Documentation
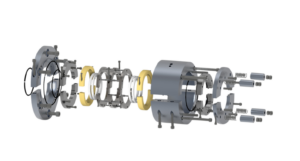
Need More Information or a Custom Quote?
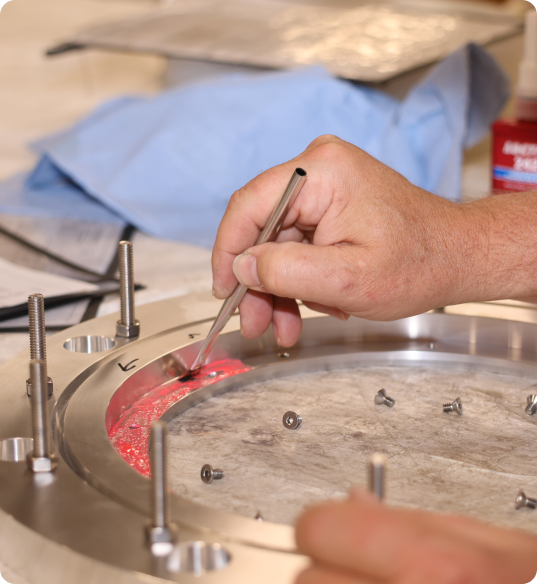